Current research projects
- An Advanced Modelling Approach for Investigating the Micromechanisms of Failure of Flexible Composite Pipes under Compression
- Application of Mixed Thermal Elastohydrodynamic Lubrication Model in Journal and Sliding Bearing Systems
- Biomimetic Tribology: Exploiting Natural Lubrication Mechanisms for Mechanical Systems
- Brain Mimicking Hydrogels
- Coarse-Grained Simulations of the Tribology of Wet Hair
- Controlling Friction Through Molecular Engineering
- Coupled Fluid-Mechanical Modelling of the Brain
- Impact of transverse vibrations on rolling-sliding lubricated contacts
- Degraded Oil Performance
- Design Principles for Low-Friction Polymer Brushes as a Synthetic Analogue of Cartilage
- Development of Novel Mechatronic Suspension Systems
- EDEN2020 (An Enhanced Delivery Ecosystem for Neurosurgery)
- Electric Vehicle Transmission Lubricant Optimisation for Efficiency and Reliability
- Finite Element Modelling of Prosthetics and Orthotics
- Fluid Flow and Mass Transfer in Brain Tissue
- Friction of 3D Printed Materials
- Friction Reduction and Optimisation of Tribological Interactions via Microtexturing and Superhydrophobic Surfaces
- Hydrodynamic Lubrication Modelling using MD-CFD Hybrid Methods
- Implementing Lubrication in Micro-Electro-Mechanical Systems (MEMS)
- Influence of Catalyst Binder Chemistry on the Microstructure of Polycrystalline Diamond During Liquid Phase Sintering
- Influence of Steel Microstructure and Composition on RCF Crack Evolution
- Infrared Microscopy to Study In-Contact Friction Behaviour
- Investigation of Tribocharging and Triboemission by Atomistic Simulations
- Lubricant Flow Inside Engines
- Lubrication and Fluid Load-Support in Hydrogels for Cartilage Substitutes
- Machine-Learning Pattern Recognition Prototype for Liquid Foams
- Mechanobiological Response of Soft Tissue
- Mechanochemical Behaviour of ZDDP
- Mechanochemistry of Lubricant Additives
- Micro-Mechanical Model Development for Predicting the Effect of Microstructure on Bulk Behaviour of Aerated Soft Solids
- Modelling Contact Fatigue Damage Using Crystal Plasticity
- Modelling Polycrystalline Diamond Cutting Tools Failure
- Modelling Transmission Efficiency in Electric Vehicles
- Molecular Simulations of Interfaces under Extreme Conditions
- Numerical Modelling of Tactile Perception
- Origins of Micropitting in Gears
- Polymeric Additives in Lubricants for Electric Vehicle Powertrains
- Prediction of Surface Initiated Rolling Contact Fatigue Cracks in Bearing Steel
- Propagation of Surface Initiated Rolling Contact Fatigue Cracks in Bearing Steel
- Scuffing in Non-Conformal Contacts
- Soot Wear Mechanisms in Diesel Engine Contacts
- Structure Breakdown During Oral Processing of Aerated Chocolates
- Surface Deposition of Carbonaceous Materials
- The Effect of Shear Stress on Lubricant Behaviour
- The Effects of Surface Texture in Reciprocating Bearings
- The Self-Assembly of Organic Friction Modifier Solutions
- Transfer Film Formation of High-Performance Polymers
- Tribofilm Properties of ZDDP-Containing Oils
- Tribology of Calcium Complex Greases
- Tribology of Wire Drawing
- Understanding and Prevention of False Brinelling Failure Mode in Rolling Element Bearings
- Understanding Viscosity Modifier Additive Performance
Researcher: Benjamin Collard
Supervisor: Prof. Daniele Dini, Dr. Finn Giuliani (Materials)
Sponsor: EPSRC and Shell (iCASE)
Summary
The research programme will employ both semi-analytical models and advanced numerical techniques to develop predictive tools for the onset of instabilities responsible for the two types of observed microbuckling mechanisms in flexible composite pipes. Effect of different fluids and environmental conditions to which these pipes are exposed will also be investigated. The research carried out will be built on the experimental programme. Understanding of the micro-mechanisms of compressive failure in fibre composite polymer systems will promote more widespread use of fibre composite pipe in existing applications and provide options for harsher environments. This will allow more effective exploitation of hydrocarbon reserves.
Supervisor: Professor Daniele Dini, Dr Tom Reddyhoff
Summary
Researcher: Murali Manoj
Supervisor: Dr Marc Masen, Dr Philippa Cann
Sponsor: NERC, Shell (Science and Solutions for a Changing Planet DTP)
Summary
The replacement of oil-based lubricants with biodegradable water-based lubricants has been a long-standing unfulfilled ambition. The physical instabilities and poor wear performance associated with water-based lubricants has led to minimal adoption within mechanical systems. However, many water-based lubrication systems exist within nature that are capable of providing extremely low friction and minimal wear.
This project aims to explore these natural lubrication mechanisms with the intention of exploiting their behaviour for application within mechanical systems. This will lead to the development of a biolubricant that is capable of providing suitable friction and wear characteristics for a multitude of applications. The biolubricant will be tuned to be compatible with materials that are likely to be adopted into many of the systems around us in the future. This allows for application of the lubricant within novel systems previously unexplored that may come to the forefront in the near future. Nature exhibits countless complex lubrication mechanisms and biological methods to achieve targeted lubrication. Hence, the focus is towards creating a biolubricant which is capable of local activation at a contact, thereby providing a local high viscosity zone with a bulk low viscosity and reducing energy losses due to churning or fluid shear. Some of the lubricant additive possibilities to be explored are proteins, cationic surfactant micelles and polymer-colloids amongst others.
Researcher: Zhengchu Tan
Supervisor: Professor Daniele Dini
Sponsor: EDEN2020
Summary
The characterisation of the mechanical response of real soft tissues, such as brain, liver and cartilage, is immensely important as it allows us to understand the way they respond under a variety of different loads. Hence, ways to reduce damage to living tissues during real life scenarios can be identified and developed. However, real tissue is difficult to obtain and test due to accessibility. Therefore, there is a huge advantage in developing an accurate synthetic tissue phantom that is easier to procure and produce. This has led to the popularity of hydrogels, which have been developed into tissue mimicking materials due to their biocompatibility and stiffness tunability.
This project focuses on the development of a composite hydrogel (CH) constituting of poly(vinyl) alcohol (PVA) and phytagel that is able to match the complex viscoelastic behaviour of brain. The CH can be tuned to achieve different stiffness and relaxation responses by varying the concentrations of each hydrogel component, which allows the material to mimic other soft tissues.
Consequently, a mechanically accurate tissue phantom material opens the doors to many applications in the study of mechanobiology and regenerative medicine. This project investigates cell viability of the CH substrate, therefore extending the range of applicability to explore a variety of different mechanical loads affects cells seeded on a CH substrate These experiments include impact tests, needle insertion tests and tribological tests to match the high strain rate behaviour of brain for the study of TBI, fracture behaviour of liver during surgery and tribological behaviour of cartilage, respectively.
Researcher: Erik Weiand
Supervisors: Professor Daniele Dini, Dr James Ewen, Dr Stefano Angioletti-Uberti (Materials)
Sponsor: EPSRC and Proctor and Gamble (iCASE)
Summary
Hair friction behavior is of particular interest for the development of hair care products. Mammal hair is formed by complex structures and requires a multi-scale approach for both experimental and numerical investigations. Despite past research efforts, the nanoscale interactions on the hair surface are not completely understood yet – particularly in the presence of hair care formulations which have been shown to drastically modify the macroscopic quantities such as the friction coefficient of hair in past
experiments.
The aim of this project is to gain fundamental knowledge on the friction behavior of human hair in the presence of coacervate formulations, as used in hair care products. Coarse-grained molecular dynamics (MD) simulations will be conducted to explore the nanoscale interactions on the hair surface in the presence of such formulations.
Researcher: Dr James Ewen
Sponsor: Royal Academy of Engineering
Summary
Lubricants help engines and other components run more efficiently by reducing friction between moving parts. This enables vehicles to use less fuel and produce fewer emissions. Improved lubricants could reduce the energy consumption and pollution from the transportation sector by up to a quarter.
Through a combination of molecular science and engineering, Dr Ewen is developing methods to design new lubricants using computational approaches. The flexible tools he develops will also be used to optimise fluids required for the moving parts in electric vehicles. Dr Ewen will collaborate closely with researchers at Shell (via the University Technology Centre for Fuels and Lubricants) and Afton Chemical as well, as university researchers across Europe.
Researcher: Andrea Bernardini
Supervisor: Professor Daniele Dini
Sponsor: EDEN2020
Summary
The brain is composed of two main types of tissues, namely grey and white matter. In this project, we focus on the latter, which is where glioblastoma is localised (i.e. where the EDEN system will infuse medication). The white matter is comprised of several types of cells and components which make it possible to theorise it as an anisotropic mechanical entity. Segmentation of the components from SEM images enables the 3-D reconstruction of the representative units to be modelled and then analysed via FEA.
A coupled fluid-mechanical model of the brain will be developed by modelling the mechanical behaviour of such tissue and its interaction with the fluidic environment in which it is submerged. This will enable the prediction of diffusive phenomena and patterns in the enhanced drug delivery in order to optimise the surgical procedure and the point of cancer-drug dosing.
Researcher: David Uribe Saenz de Camara
Supervisor: Amir Kadiric, Daniele Dini
Sponsor: SKF
Summary
Rolling-element bearings are one of the most abundant machine components found in mechanical systems. There is a rising demand for an improved performance, higher efficiency and longer service lives. The reliability of rolling bearings has increased considerably over the last decades, and yet there are circumstances when they fail prematurely, well short of their rated life.
The aim of this project is to improve the fundamental understanding of surface damage and EHL effects that may occur when lubricated rolling-sliding contacts are subjected to transverse vibrations. This would in turn help to improve bearing performance in relevant applications such as wind turbines. Damage accumulation experiments will be performed using a triple-disc rolling contact fatigue rig, under closely controlled laboratory conditions in the elastohydrodynamic and mixed lubrication regimes.
For this purpose, a new test rig setup capable of imposing transverse vibrations has been developed. A powerful electrodynamic modal shaker is used to impose vibrations for a wide range of amplitudes and frequencies along with an in situ lubrication condition monitoring system.
Date Started: October 2019
Researcher: Mohamed Abdelbar
Supervisor: Prof. Daniele Dini, Dr Stefano Angioletti-Uberti, Dr James Ewen
Summary
The articular cartilage found covering the ends of bones in the synovial joints of mammals exhibit exceptional tribological properties, giving a low friction response (μ = 0.001) even when subjected to normal loads exceeding 100 atm. The goal of this project is to use coarse-grained molecular dynamics in order to study the system focusing on the architecture of the polymers on the surface and thus provide rational design principles for cartilage analogues.
Researcher: Dr. Min Yu
Supervisors: Professor Daniele Dini
Sponsor:
Summary
Experimental and road testing of Series Active Variable Geometry Suspension (SAVGS) and the Parallel Active Link Suspension (PALS).
Researcher: Dr Stefano Galvan, Andrea Bernardini, Zhengchu Tan
Supervisor: Professor Daniele Dini, Dr Philippa Cann, Dr Marc Masen
Sponsor: EDEN2020
Summary
Due to an aging population and the spiralling cost of brain disease in Europe and beyond, EDEN2020 aims to develop the gold standard for one-stop diagnosis and minimally invasive treatment in neurosurgery. Supported by a clear business case, it will exploit the unique track record of leading research institutions and key industrial players in the field of surgical robotics to overcome the current technological barriers that stand in the way of real clinical impact.
Researcher: Alexander MacLaren
Supervisor: Dr Amir Kadiric, Prof. Hugh Spikes
Sponsor: Valvoline
Summary
Extending the range of Electric Vehicles (EVs) is the principal challenge faced by manufacturers in outcompeting existing Internal Combustion Engine (ICE) powered vehicles, as they prepare for the energy transition. The much greater powertrain efficiency of EVs compared to ICEs has brought gearbox efficiency into the spotlight in the push to further increase powertrain performance.
The prevailing trend of decreasing lubricant viscosity to reduce tractive and churning losses in gearboxes results in new failure modes for gears driven by electric motors capable of delivering their maximum torque at very low speeds. New water-based formulations acting as both coolant and lubricant further compound these reliability issues, and bring the electrochemical properties of the lubricant into question. Innovative gearbox lubricants must therefore balance the conflicting requirements of efficiency and reliability.
This project will determine the effects of water-based lubricants both on efficiency and reliability in EV gearbox applications, and explore a new generation of triboelectrochemically active additives in optimising lubricant performance.
Researcher: Jack Hayes
Supervisor: Dr Marc Masen, Claire Higgins (Bioengineering) and Peter Worsley (Southampton)
Sponsor: EPSRC Centre of Doctoral Training (CDT) in Prosthetics and Orthotics (P&O)
Summary
This project will study the effect of contact pressures on residuum-socket interactions. Finite Element Modelling (FEM) will be used to inform redesign with regards to socket geometry and material parameters.
Researcher: Tian Yuan
Supervisor: Prof. Daniele Dini, Dr Marc Masen
Sponsor: China Scholarship Council and Imperial College London
Summary
This project is to investigate how drug fluid flows inside the brain and how the drug particles diffuse
within the fluid domain in order to improve the therapy name Convection-Enhanced Delivery (CED)
for the treatment of brain diseases. The research works are mainly focused on numerical modelling
but also involve experimental validations. Arbitrary Lagrangian Euler (ALE) method is used to
describe the Fluid-Solid Interaction (FSI) between drug fluid and neuron cells and Finite Element
Method (FEM) is used to solve the deformation of the neuron cells and the fluid flow in the brain.
The interaction between drug particles and neuron cells will be calculated based on molecular
modelling. Experiments at different scales will be done as well to validate the simulations. With this
establishment of this modelling framework, the influence of factors that affect the efficiency of CED
will be clear and this therapy could be improved. This numerical model could also serve as a
consultant for the surgical preparation.
Supervisor: Dr Tom Reddyhoff
Sponsor: EPSRC
Summary
Wear control, which relies on understanding the mechanisms of wear, is crucial in preserving the life of mechanical components and reducing costs. Additive manufacturing (AM) techniques can produce parts with tailored microstructure, however, little has been done to understand how this impacts the mechanisms of wear.
In this project we study the impact of initial grain arrangement and crystal orientation on the wear mechanisms of austenitic stainless steel (SS) in dry sliding contact. Specifically, the anisotropic sliding wear behavior of as-built, AM-ed 316L SS is compared against annealed, wire-drawn counterparts.
Researcher: Jun Wen
Supervisor: Dr Tom Reddyhoff, Prof. Daniele Dini
Sponsor: China Scholarship Council and Imperial College London
Summary
The aim for this PhD project is to reduce friction in hydrodynamic bearings using surface treatments. The application will be targeted first is micro-scale bearings to explore the lubrication of Micro-Electro-Mechanical-Systems (MEMS). Due to the small size and the functions they can perform, MEMS devices have the potential to significantly impact our way of life, but are currently limited by severe problems of friction and wear that occur at the micro-scale.
To address this problem, the way of entrapping air pockets on the bearing surfaces by surface modification will be used. An important and highly novel aspect of the project will be to use silicon fabrication techniques, including Deep Reactive Ion Etching (DRIE), to produce surface features which will act to anchor the gaseous regions in place. Then, the models of bubble interface interactions will be combined with the hydrodynamic bearing lubrication model in order to validate and optimize the experimental results. This will also help to explore the possibility of bubble/cavitation induced friction reduction in other application such as macro-scale hydrodynamic bearings.
Researcher: Eduardo Ramos Fernandez
Supervisor: Professor Daniele Dini, Professor David Heyes, Dr Edward Smith
Sponsor: BP, Theory and Simulation of Materials (TSM-CDT)
Summary
The field of nanotribology has remained slightly detached from mainstream macro-scale tribology, focusing primarily on specialized nano-scale applications. At the macro- and mesoscopic levels, continuum models are often able to correctly model fluids. However, at smaller scales, continuum models do not consider the atomic nature of matter and can sometimes fail to capture the essential physics. In such cases, explicit molecular models must be employed, for example to model a liquid-solid interface.
The development of a truly multi-scale approach, which spans nano- to macro-scales, is a decisive step forward in understanding engineering tribological interfaces. Hybrid methods, where atomistic simulations such as molecular dynamics (MD) and continuum computational fluid dynamics (CFD) inter-operate, offer a solution that combines the strengths of both paradigms. The aim of this project is to model contact-lubrication problems with a multi-scale simulation methodology taking advantage of an in-house coupling software (CPL_library) that has been developed in the group in the past years.
Researcher: Peng Wang
Supervisor: Dr Tom Reddyhoff
Sponsor: Imperial College London
Summary
Micro-electro-mechanical systems (MEMS) are tiny (sub-millimetre) machines, which have arisen from advances in semiconductor fabrication. Due to their low cost, high tolerances, and ability to combine sensors and actuators with microprocessors, MEMS have the potential to profoundly affect our way of life. However, high friction and wear problems mean that current commercial MEMS designs are confined to non-, or very low sliding devices.
This project aims to demonstrate how low viscosity liquids combined with friction modifier additives are an effective means of the lubricating MEMS devices. This has so far only been achieved in lab-based tests; therefore the current aim is to implement this type of lubrication in an actual MEMS device. To do this, the project is using semiconductor fabrication techniques to build micro-hydrodynamic bearings which will be incorporated and tested in a MEMS turbine energy harvester.
In addition to the goal of producing a MEMS turbine that runs on hydrodynamic micro-bearings, a number of more fundamental avenues of research, involving tribology and silicon MEMS, are being explored. These include a feasibility study into the development of sliding MEMS with textured surfaces.
This project is a collaboration with the Optical and Semiconductor Devices Group at Imperial College.
Researcher: Branislav Dzepina
Supervisor: Professor Daniele Dini
Sponsor: Element Six
Summary
The main problem of polycrystalline diamond cutters (PDCs) used in oil and gas drilling is the brittle nature of the diamond cutting face. Premature fracture during a drilling operation results in ineffective rock cutting. Repair of the fractured cutters requires complete removal of the drill head and string. The subsequent down-time imposes a great monetary burden to the driller. It is thus important to be able to manipulate the behaviour of the cutter to prevent or delay the onset of long cracks which lead to catastrophic brittle failure.
One possible way to affect the properties of the diamond cutter is through manipulation of the microstructure. To this end, the project proposes the development of a Monte Carlo model to simulate the evolution of the microstructure during high-pressure high-temperature (HPHT) liquid phase sintering. In order to enable inputs for the model, molecular dynamics simulation and HPHT experimentation will be conducted. It is anticipated that the proposed simulation will not only identify new mechanisms for the diamond sintering model, but also allow microstructural prediction given key input variables.
This project forms part of the Diamond Science and Technology CDT.
Researcher: Chiara Bertuccioli
Supervisor: Amir Kadiric, Finn Giuliani
Sponsor: SKF
Summary
Rolling contact fatigue (RCF) involves initiation and subsequent propagation of cracks due to cyclic stresses caused by a rolling-sliding contact, which eventually leads to the creation of a surface pit and component failure. RCF is a life-limiting failure mode of many engineering components including rolling bearings, gears and cams. Despite its obvious practical and economic importance, the fundamental mechanisms behind RCF are not fully understood.
The overarching aim of this project is to gain a fundamental understanding of the mechanisms that drives crack initiation and early propagation implementing the use of modern analytical techniques to study the material’s microstructural effects on RCF mechanisms.
Date Started: October 2018
Researcher: Jia Lu
Supervisor: Dr Tom Reddyhoff, Professor Daniele Dini
Sponsor: Imperial College London
Summary
The overall aim of this PhD project is apply infrared microscopy to a range of sliding interfaces in order to increase our understanding of the in-contact mechanisms that give rise to heat generation.
The first task is measuring the temperature distribution of the oil within an elastohydrodynamic contact. This involves using an infrared camera and microscope with a number of filters to record the radiation emitted from a contact between a metal ball and transparent sapphire disc. The radiation data obtained in this way is calibrated and processed using Planck’s Law and combined with film thickness measurements in order to separate the temperature of the two bounding surfaces from that of the film of oil.
Once achieved, results will then be used to test theories that predict oil temperature rheology.
In addition to, effect of surface coatings and lubricant additives on in-contact temperature and rheology will be studied using this technique.
Researcher: Dr Alessandra Ciniero
Supervisor: Dr Tom Reddyhoff, Prof. Daniele Dini
Sponsor: EPSRC
Summary
The aim of this project is to investigate the mechanisms by which phenomena known collectively as “triboemission” (i.e. the emission of photons electrons and charged particles due to rubbing) occur. This is important because triboemission may be responsible for certain tribochemical processes such as lubricant degradation. Ab intio molecular dynamics techniques will be used to model tribocharging and triboemission during sliding.
Researcher: Bastien Bolle
Supervisor: Dr Janet Wong, Prof. Pavlos Aleiferis
Sponsor: Shell
Summary
The aim of the project is to investigate the flow of lubricants inside internal combustion engines.
Researcher: Elze Porte
Supervisor: Dr Marc Masen, Dr Philippa Cann
Sponsor: Imperial College London
Summary
This research focuses on gaining a better understanding of the lubrication mechanisms in articular cartilage. Currently, there is no thorough understanding of the relationship between the lubrication of the material, its fluid load support, and its mechanical properties.
Hydrogels have been suggested as promising substitute materials for cartilage because of their specific mechanical and tribological properties. This makes them suitable substitutes for use in lubrication experiments and, ultimately, as a potential cartilage replacement material in the surgical treatment of osteoarthritis
Fluid exudation from the bulk material into the loaded region is believed to provide the fluid load support and lubrication. To study the lubricating mechanisms of hydrogels as cartilage substitutes, contact and lubrication experiments are done on the newly developed Biotribometer (PCS Instruments, London UK). The obtained knowledge can be used to improve the existing hydrogel structures.
Researcher: Dr Li Shen
Supervisor: Professor Daniele Dini, Dr Tom Reddyhoff
Sponsor: EPSRC, Shell, PCS Instruments, Ab InBev, PespsiCo
Summary
This project is an EPSRC Impact Acceleration Account (IAA) entitled “Machine-Learning Pattern Recognition Prototype for liquid foams”. The IAA grant supports the development of a potentially marketable project to create impact away from a strictly academic setting. The project aims to develop a foaming rig and a Machine-Learning analysis algorithm that will enable a consistent quantitative analysis of the foaming process in beverages and oil lubricants.
Researcher: Luli Li
Supervisor: Dr Marc Masen
Sponsor: EPSRC
Summary
This project focuses on studying the contact mechanics of tissue. The project aims to measure the mechanobiological response of soft tissue using cytokines, following interaction of tissue with devices or implants. The research will combine tribometer experiments and Finite Element Modelling (FEM).
Researcher: Dr Jie Zhang (Jason)
Supervisor: Professor Hugh Spikes
Sponsor: EPSRC, Afton Chemical
Summary
It has recently been shown that tribofilm formation by the widely-used antiwear additive zinc dialkyl dithiophosphate (ZDDP) is driven by the applied shear stress present in rubbing contacts rather than by the energy dissipated in these contacts. This means that ZDDP reaction results from the stretching and breaking of molecular bonds under stress, i.e. mechanochemistry; an insight that enables relationships between molecular structure and reactivity to be developed. This project studies the impact of applied shear stress on ZDDP film formation under both full film and boundary lubrication conditions to support the principle that ZDDP reaction is controlled by mechanochemistry.
Researcher: Carlos Ayestarán Latorre
Supervisors: Professor Daniele Dini, Professor Hugh Spikes, Dr James Ewen
Sponsor: Afton Chemical, TSM-CDT
Summary
The aim of this project is to utilise molecular simulations to investigate the mechanochemical behaviour of lubricant additive molecules. Classical molecular dynamics simulations will be employed to study the stresses on additive molecules under shear. First-principles modelling frameworks will also be developed to accurately model lubricant reactivity in order to study their breakdown inside tribological contacts. By understanding the mechanochemical breakdown of current additives new and more effective additives can be designed from the molecular level.
Researcher: Georgios Samaras
Supervisor: Dr Philippa Cann, Dr Marc Masen, Prof Maria Charalambides, Prof Yannis Hardalupas
Sponsor: Nestlé
Summary
Soft food systems are often used in confectionery products, such as emulsion or foam fillings, to provide consumers with a unique experience. Traditionally, the mechanical and rheological properties of these systems are studied in combination with sensory evaluation to describe their in-mouth flow properties. However, oral processing of food is very complex and several multi-scale mechanisms take place at the same time in the mouth. This is especially noticeable when dealing with more complex systems, e.g. when hard particles (inclusions) are included within a semi solid system, or products with different micro- and macroscopic structure, e.g. aerated systems. This hinders predictions of the in-mouth behaviour of the food. Knowledge of this behaviour is crucial as it is directly linked to sensory perception.
The aim of the project is to develop a multi-scale thermo-mechanical computational model for simulating the interaction between aerated fluid and solid structures. This includes first bite model for fracture and progressive damage of product into particles and subsequent shearing of particles in tongue/palate contact whilst they heat up, flow, mix with saliva and form cohesive bolus. Necessary rheological experiments, in compression and shear of boluses, will be developed to provide data for validating simulations.
Researcher: Xikai Yu
Supervisor: Amir Kadiric, Daniele Dini, Fionn Dunne
Sponsor: SKF
Summary
The aim of this project is to simulate surface and subsurface crack initiation in bearings and develop local fatigue damage criteria with crystal plasticity finite element (CPFE) method. The approach is able to account for the effects of material microstructure including the effects of grain morphology, anisotropic material properties and slip activities. The project is closely linked to another PhD at Imperial which is studying the RCF crack evolution with different material microstructures using experimental methods. The project aims to provide a better understanding of grain-scale mechanisms of crack initiation and therefore to contribute to better predictions of fatigue lifetimes of rolling bearings.
Date Started: December 2019
Researcher: Mahdieh Tajabadi Ebrahimi
Supervisor: Professor Daniele Dini, Dr Daniel Balint, Professor Adrian Sutton FRS
Sponsor: Element Six, Theory and Simulation of Materials (TSM-CDT)
Summary
Element Six (E6) is the world's leading manufacturer of synthetic diamond for hard abrasive materials. Synthetic diamonds are used throughout many industrial applications such as cutting, grinding, drilling, and polishing. Polycrystalline diamond (PCD) is one of the E6 products that is formed by sintering diamond powders in the presence of the metallic catalyst. PCDs fail by cracking of diamond crystals under extreme conditions. The theory of fracture, indicates that the dislocations, impurities, and any imperfections present inside the diamond grains can affect their mechanical properties. PCDs contain various imperfections that might cause failure by producing nano-cracks in the system. The objective of the project is to shed light on the mechanisms that lead to these failures, involving different scale. Techniques at different length scale will be used to characterise possible mechanisms of nano-cracks initiation and propagation into macro-cracks inside the system.
Researcher: Joseph Shore
Supervisor: Dr Amir Kadiric, Prof. Daniele Dini
Sponsor: Valvoline
Summary
Range extension is one of the most important research areas in the development of Electric Vehicles (EVs). Current EVs have significantly shorter ranges per battery charge than a typical Internal Combustion Engine (ICE) vehicle has with a full tank. This, along with consumer concerns regarding lengthy charge times and limited charging point availability has limited the penetration of EVs into the market. Although improvements in battery technology has significantly improved vehicle range in recent years, we are approaching the theoretical maximum energy density achievable with lithium-ion batteries. Therefore, we must look elsewhere to improve range. Improving transmission efficiency is one way to do this.
In conventional ICE vehicles, power losses are dominated by the engines, which typically have efficiencies below 40%. In comparison, Electric Motors (EMs) have efficiencies in the 90% range. Transmission losses therefore make up a much greater proportion of the overall vehicle losses than in ICE vehicles, being the second greatest source after battery charging. Therefore, improvement in transmission efficiency could significantly exchange vehicle range. There are a number of challenges when selecting components and lubricants for an EV. The torque-speed characteristics of EMs are significantly different to ICEs and the higher speeds achieved by EMs result in significant churning losses. These high speeds also result in significant shear heating, reducing the lubricant viscosity and increasing the risk of component failure.
EMs typically operate at maximum torque near zero speed and as such, the need of a clutch is negated. The torque-speed characteristics of EMs also allow EV transmissions to operate with just a single ratio gear reduction, greatly simplifying the design. However, the transmission will therefore be required to run at a much wider range of input speeds than an ICE vehicle transmission. This presents challenges when selecting a lubricant, as any chosen lubricant must have a significant enough viscosity to enable it to provide an adequate film thickness at lower speeds, whilst not being so viscous as to cause excessive churning losses at high speeds.
The aim of this project is to develop an accurate computational model to predict the different losses in EV transmissions, including gear losses, bearing losses and churning losses. This will provide a valuable design tool for automotive manufacturers, allowing them to better optimise transmission designs and thereby improve the vehicle range.
Supervisors: Professor Daniele Dini, Dr James Ewen
Sponsor: Baker Hughes
Summary
The molecular-level interactions between lubricants and engineering surfaces are not fully understood. The aim of this project is to conduct molecular simulations to investigate the behaviour of lubricated surfaces under extreme temperature, pressure, and sliding velocity conditions. An understanding of this behaviour is required to design advanced materials and molecules for drilling applications. The ultimate goal is to develop a true multi-scale (atomistic to continuum), multi-physics tribological model for drilling problems.
First, molecular simulations will be conducted on existing well-defined systems of lubricants and surfaces under thermomechanical loading to study their effectiveness and breakdown. With this initial framework in place, it will be used to accelerate future development and yield effective formulated lubricants and engineered surfaces for drilling applications.
Supervisor: Dr Marc Masen, Professor Daniele Dini
Summary
We are numerically modelling skin-surface interaction in order to better understand the sensations of touch and perception. The project involves developing finite element models and utilising data science methods to evaluate the stress, strain and energy fields within multi-layered hyper/viscoelastic soft tissue in the vicinity of mechanoreceptors. A better understanding of the processes of tactile perception and mechanotransduction have applications in a variety of fields, from the development of new skincare products, to the tailoring of product/surface engineering methods.
Researcher: Benjamin Wainwright
Supervisor: Dr Amir Kadiric
Sponsor: Mitsubishi
Summary
Micropitting is a form of rolling contact fatigue associated with hardened gears and rolling element bearings. It consists of microscopic pits on the scale of surface asperities which can cover large areas on surfaces of the gear tooth flanks and bearing raceways. This can lead to sever loss of material and provide an initiation point of other types of rolling contact fatigue such as macropitting. The mechanism by which micropitting leads to significant material degradation is not well understood and there is a need to produce universally accepted design guidelines to predict the useable life of machine components.
Experiments are being undertaken on a PCS Micropitting Rig (MPR) complimented through the development of numerical tools to aid in better understanding and predicting micropitting damage.
Researcher: Amran Mohamed
Supervisor: Dr Janet Wong, Dr Luca di Mare (Oxford), Dr James P. Ewen
Sponsor: EPSRC, Shell (Science and Solutions for a Changing Planet DTP)
Summary
This project will use computer simulations to investigate the effect of VM molecular architectures on their stability and behaviour in lubricants in ranges of temperature, shear rates, and contact surfaces encountered in EV. Dissipative particle dynamics (DPD) simulations will be used. DPD method is a coarse grain method that allows simulations to be conducted in length scale and time scale that are close to those encountered in tribological contacts. The goal is to establish relationship among molecular architecture of additives, their stability and effectiveness. The knowledge can that be used to guide VM design for EV lubricants.
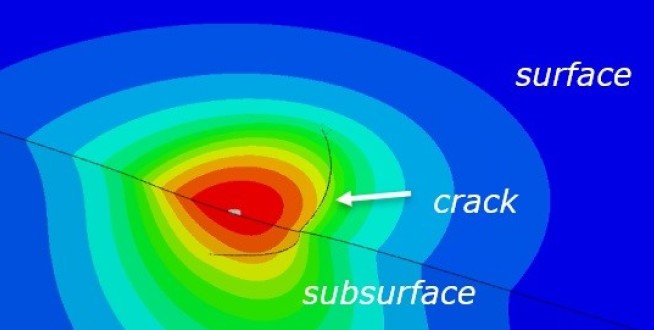
Researcher: Bjoern Kunzelmann
Sponsor: SKF
Supervisor: Amir Kadiric, Daniele Dini
Summary
Surface initiated rolling contact fatigue, leading to a surface failure known as pitting, is a life limiting failure mode in many modern machine elements, particularly rolling element bearings. This project builds on previous work at Imperial College which for the first time identified two phases of RCF crack propagation which leads to pitting failure in the ultimate stage. Phase I crack propagation is associated with shorter cracks (<100µm) and exhibits relatively slow crack propagation rates with frequent crack arrests whereas phase II is associated with longer cracks (>100µm) which show rapidly increasing crack growth rates following a Paris like power law [1].
A triple-disc contact machine is used to determine the major parameters which influence rolling contact fatigue crack growth including surface topography, fluid crack interaction, contact size etc. In parallel, a three-dimensional numerical crack model (Figure 1) has been developed which is able to predict stress intensity factors for crack morphologies which were observed in the experiments. Furthermore, the numerical model accounts for effects such as crack face friction and fluid pressurisation in the crack which can have significant effect on stress intensity factors experienced at the crack tip. This study focuses on the prediction of rolling contact fatigue crack growth with linear elastic fracture mechanics (LEFM). As most of the rolling contact fatigue lifetime is consumed by crack propagation the prediction of the crack growth with LEFM allows the estimate of the residual bearing life after crack detection. A combined numerical and experimental approach is used in order to determine the major influencing parameter for different operating conditions and hence contribute to development of better contact fatigue lifetime predictions.
[1] P. Rycerz, A. Olver, and A. Kadiric, “Propagation of surface initiated rolling contact fatigue cracks in bearing steel,” Int. J. Fatigue, vol. 97, pp. 29–38, 2017
Date Started: July 2018
Researcher: Dr Pawel Rycerz
Supervisor: Dr Amir Kadiric, Professor Andrew Olver
Sponsor: SKF
Summary
Surface initiated rolling contact fatigue, leading to a surface failure known as pitting, is a life limiting failure mode in many modern machine elements, particularly rolling element bearings. Most research on rolling contact fatigue considers total life to pitting. Instead, this work studies the growth of rolling contact fatigue cracks before they develop into surface pits in an attempt to better understand crack propagation mechanisms.
A triple-contact disc machine will be used to perform pitting experiments on bearing steel samples under closely controlled contact conditions in mixed lubrication regime. Crack growth across the specimen surface will be monitored and crack propagation rates extracted. The morphology of the generated cracks will be observed by preparing sections of cracked specimens at the end of the test.
Researcher: Bo Peng
Supervisor: Dr Amir Kadiric
Sponsor: SKF
Summary
Scuffing is a surface failure mode that occurs in sliding-rolling contacts subjected to high loads and high sliding speeds, such as those in gears and cam-followers. Owing to its sudden onset, rapid progression and dependence on both fluid and boundary lubricant films, scuffing is difficult to study in a repeatable manner. In this project, we will develop a scuffing test method based on contra-rotation. We will extend the method to higher loads using a new experimental set-up and apply it to study the onset of scuffing with a selection of model and fully-formulated lubricants.
Researcher: Thomas Kirkby
Supervisor: Dr Tom Reddyhoff
Sponsor: Volvo Trucks
Summary
The project investigates the mechanisms by which soot causes problematic wear in heavy-duty diesel engine components. This is important since understanding soot mediated wear can allow for an increase in the amount of soot in engine oils. This will enable vehicles to achieve an optimum CO2 - NOx trade-off, and hence lower emissions. Current industry standard lubricant tests for used oil fail to predict soot related wear problems in real engines and therefore new analytical techniques are required. To address this, this PhD project develops a range of lab-based tests characterising oil properties and comparing with friction and wear measurements. Results from this form part of an industrial programme utilizing real field data.
Researcher: Dimitrios Bikos
Supervisor: Dr Philippa Cann, Dr Marc Masen, Prof Maria Charalambides, Prof Yannis Hardalupas
Sponsor: Nestlé
Summary
Aerated chocolate products are popular consumer items associated with positive textural and sensory attributes. Among other microstructural features such as cocoa solids, sugar particles, etc. aerated chocolate consists of bubbles as well. Interaction between bubbles and particles occur during the structure build-up and structure breakdown process and therefore it needs to be investigated. Therefore, a multidisciplinary approach is taken to predict how microbubbles impact on the rheological, thermal and lubrication processes through progressive structure breakdown in the mouth. However, the effect of the aerated microstructure on the chocolate’s behavior during both industrial and oral processes is a very complex research field. During oral processing, food first fractures into particles, which interact with saliva to form a bolus, which is then swallowed. During this process, mechanical and thermal loads are applied whilst the effect of the contact with the oral cavity is also crucial in determining the consumer’s taste experience. Chocolate changes phase as it melts further complicating the behavior. However, the effect of aeration on industrial processing or manufacturing of chocolate cannot be neglected. Specifically, the effect of bubbles on the thermal properties of the chocolate is to be determined such that manufacturing can be controlled to ensure that chocolate will have the desirable textural and sensorial attributes.
Researcher: Dr Sophie Campen
Supervisor: Dr Janet Wong
Sponsor: BP
Summary
Fouling by carbonaceous deposits poses a serious and costly problem for the oil production industry. In upstream, midstream and downstream oil production, carbonaceous deposits frequently consist of asphaltene. Asphaltene is the densest, most polar fraction of crude oil and is generally stable in the reservoir. However, changes in environmental conditions, in particular pressure, but also temperature, shear rate and solvency of the crude oil base stock can lead to asphaltene being destabilised. Destabilisation of asphaltene, resulting in its precipitation from liquid crude is believed to be responsible for the formation of thick deposits that can completely plug the wellbore. Asphaltene is defined by its solubility: soluble in aromatic solvents like toluene, but insoluble in n-alkanes like heptane. Being a solubility class of compounds means that by definition, asphaltene is polydisperse. This makes cross-study comparisons challenging since crude oils from different sources possess different chemistries and hence display different deposition behaviours.
The aim of this project is to achieve a fundamental understanding of the mechanisms that govern asphaltene deposition. This will allow for better informed decisions on the most effective pathways to preventing fouling, for example through additive chemistry and smart surface coatings. Asphaltene deposition will be investigated experimentally using a quartz crystal microbalance. This technique allows us to measure in situ the deposited mass as a function of time.
Funded by BP, this study forms part of larger project within the International Centre for Advanced Materials and involves collaboration with partner members at Imperial College London, the University of Manchester, the University of Cambridge, and the University of Illinois at Urbana-Champaign.
Researcher: Stephen Jeffreys
Supervisor: Dr Janet Wong, Professor Hugh Spikes
Sponsor: Shell
Summary
The aim of the project is to investigate the effect of shear stress on lubricant behaviour, particularly in high-pressure high-shear environments such as those found in elastohydrodynamic (EHD) contacts. Here it is critical to gain an understanding of the rheological properties at a molecular level, considering the local structure of the lubricant. Given the severity of operating conditions lubricants can reveal unusual phenomena where the Newtonian assumption may be inadequate. An inaccurate description of the flow limits our understanding of lubricant rheology which affects the ability to theorize novel ways of controlling friction. This impacts the overall goal to manipulate the tribological performance of engineering systems and improve efficiency.
Researcher: Dr Sorin-Cristian Vladescu
Supervisor: Dr Tom Reddyhoff
Sponsor: Ford Motor Company
Summary
The research project is conducted in collaboration with the Ford Motor Company, and evaluates the how textured surfaces, produced using Laser Surface Texturing (LST), can improve the tribological performances of an internal combustion engine components. Particular focus is on the reciprocating contact between the cylinder liner and piston rings, since this accounts for the approximately 4% of the overall fuel energy used.
To achieve this goal the project involves simultaneously measuring friction force and film thickness in a reciprocating contact using a test rig designed specifically for this purpose. A range of pocket configurations on the ring-liner pairing are investigated, in order to identify an optimum texture pattern suitable for actual piston ring conditions and also to shed light on the mechanisms that are occurring.
Researcher: Ben Fry
Supervisor: Dr Janet Wong, Professor Hugh Spikes
Sponsor: Croda
Summary
Organic friction modifiers (OFMs) are used to reduce friction in the boundary regime. This happens through self-assembled monolayers (SAMs) of the OFMs onto the surface. This project looks at the formation and properties of the SAMs in idealised systems and relate them to friction data to get a better understanding of the mechanism of the OFMs friction reducing properties.
The main techniques to observe the structure and growth of these monolayer are atomic force microscopy (AFM) and spectroscopic ellipsometry. With these combined techniques, a picture of how the monolayer is formed on the surface from a dilute solution can be created.
Researcher: Kian Kun Yap
Supervisor: Dr Marc Masen, Dr Janet Wong
Sponsor: DuPont
Summary
A metal-polymer sliding interface can self-lubricate due to the transfer film formation mechanism. It is therefore ideal for applications where liquid lubricants are inapplicable, for example, in the aerospace, pharmaceutical, and semiconductor industry. It is well known that linear polymers such as PTFE and UHMWPE can form thin and stable transfer film which is excellent in friction reduction. However, most high-performance polymers (HPPs) have highly complex chemical structures and hence do not obey the oversimplified textbook explanation for the transfer film formation mechanism. This project aims to elucidate the transfer film formation of HPPs and specifically polyimides, utilising in-situ and real-time surface characterisation techniques (e.g. spatiotemporal mapping as shown in the figure) during the polyimides/stainless steel sliding. With the support from DuPont, the chemical properties of polyimides can be customised as a strategy to better understand the fundamental mechanism of self-lubrication.
Researcher: Mao Ueda
Supervisor: Professor Hugh Spikes
Sponsor: Shell
Summary
Zinc dialkyl dithiophosphate (ZDDP) is widely used as an anti-wear additive in engine oils. The tribofilms formed by ZDDP have been extensively investigated using friction and wear tests as well as surface analysis. However, the influence of ZDDP film properties on film durability and ultimately tribological performance remains unclear. The aim of this project is to uncover these relationships, as well as to investigate the effect of co-additives on ZDDP performance.
Researcher: Rory McAllister
Supervisor: Dr Phillipa Cann, Dr Marc Masen
Summary
Electrification of the automotive sector is putting even more emphasis on low-friction bearing lubricants, and the burgeoning battery market has driven up the price of lithium, a raw material in >70% of lubricating greases. There is, therefore, a need to replace the standard lithium grease thickener with a cheaper, equally effective alternative.
This project aims to investigate the performance of novel calcium complex grease formulations provided by Shell. Rolling contact tests will be performed with both lubricant degradation and inlet starvation controlled to emulate realistic bearing conditions. Techniques such as infrared spectroscopy will be used to analyse the rolled tracks in order to understand the mechanisms of grease lubrication.
Researcher: Marie-Louise Schlichting
Supervisor: Dr Marc Masen, Dr Amir Kadiric
Summary
Tribology plays an important role in metal-forming processes. In particular in wire drawing, tribological conditions are of great significance, as this process involves high speeds, high pressures and large plastic deformation. Wire Drawing is a widely used metal-forming process to produce wires, particularly thin wires. It is the process of pulling a wire through a conical die to reduce its cross-sectional area. At the contact between wire and die, the wire is subjected to high frictional forces. This affects wire quality, energy consumption as well as die life, and subsequently productivity. To reduce friction, lubrication can be added to the contact. In general, rather unconventional lubricants such as emulsions or metal soaps, are used in wire drawing. However, the tribological conditions in high speed drawing with high pressures and these unconventional lubricants are hardly studied. This work investigates the underlying tribological conditions in wire drawing.
Researcher: Rachel Januszewski
Supervisor: Dr Amir Kadiric
Sponsor: SKF
Summary
False brinelling is a type of surface damage that most commonly occurs in non-conformal, nominally stationary contacts that are subjected to externally generated vibration. All machine elements that rely on non-conformal, rolling-sliding contacts in their operation can suffer from false brinelling, but it is most commonly observed in rolling element bearings, especially in stand-by equipment stored near running machines and in the transport of automotive vehicles by rail or sea.
False brinelling is a specific type of a more general contact damage mechanism of fretting, often referred to as fretting corrosion. The underlying mechanisms causing fretting and false brinelling are thought to be similar, but false brinelling in rolling bearings has an added complication that the oscillatory motion is not pure sliding but also involves rolling of rolling elements on bearing raceways.
The aim of the proposed research is firstly, to gain a better understanding of the factors that drive the onset and progression of false-brinelling damage and secondly, to provide potential preventative measures, be it through the improvements in bearing design or lubricant formulation.
Researcher: Eliane Gendreau
Supervisor: Dr Janet Wong, Professor Hugh Spikes
Summary
Viscosity modifiers are polymers added to lubricants to control viscosity. Effective viscosity modifiers are crucial in the automotive industry to facilitate the use of base oils with lower viscosity which can reduce hydrodynamic losses and thus increase fuel efficiency. The aim of the project is to investigate how the architecture of polymeric viscosity modifiers affects lubricant rheology. Techniques such as fluorescence spectroscopy will be used to study the effect of polymer architecture on thier temperature and shear responses inside hydrodynamic contacts.