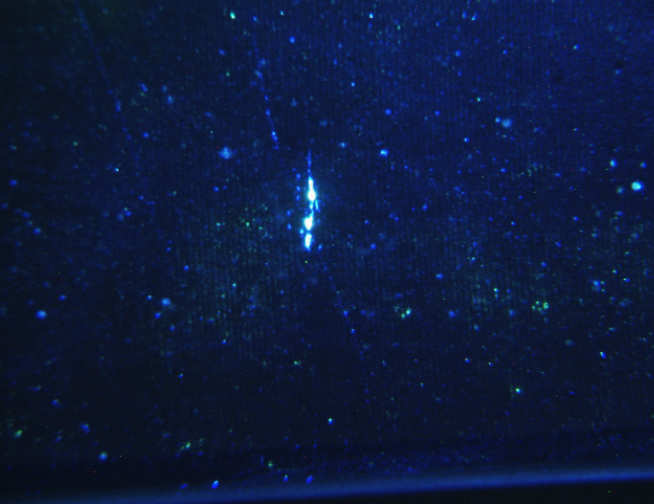
A high proportion of current non-destructive evaluation (NDE) methods output image based results. Such methods include penetrant inspection, magnetic particle inspection and radiographic testing. Currently, image based results, such as those previously mentioned, require a user to look at the processed part (or an image of a processed part) to determine if there are any defects present. As well as this being costly and time consuming, it leaves the analysis open to human error. The success of the inspection is to a large extent due to the inspector. In methods such as radiographic testing, there is some degree of accountability, as physical images are taken and stored for a specified length of time. However, for methods such as penetrant inspection and magnetic particle inspection, the individual components are passed down the process line, and at the end are each inspected by an inspector. If the part is deemed to be defect free, it is passed on to the next part of the manufacturing or servicing line as appropriate. This could have catastrophic effects if a part containing a defect goes unnoticed and hence is allowed to continue in service.
The aim of this project is to remove human input in as larger extent as possible. There are two main parts to the project, the first being the development of a technique to obtain images which permit the analysis of the entire surface of the part.
The second part of the project will be to develop the computer software to detect the presence of cracks in images that are often noisy. Figure 1 shows one of the more clear images of defects obtained using fluorescent penetrant inspection (FPI). The project will build on existing image capture and machine learning systems being researched at Rolls Royce and the University of Manchester to establish reliable detection techniques without numerous false detections.
Funding Sources and Sponsors
EP/L015587/1 (EPSRC Centre for Doctoral Training in Quantitative NDE)
Rolls Royce plc